Painting with Fire
The conversion from clay to ceramics can be fuelled by so many different methods and the variables are infinite. I always find it so intriguing to observe these stories that each pot tells us about its making and maker. With one such unique firing planned I was headed to Golden Bridge Pottery in Pondicherry, to fire the only Anagama Kiln we have in India. Since Covid being an evident part of our lives now, this was the first time I was heading out after over a year. With a mixture of giddiness, anxiety and excitement we were off on our adventure.

Appreciating the change of place and pace, I was feeling super grateful for the opportunity. I took sometime exploring new techniques and tools out of my usual ways of making. The first few days were spent working with the beautiful stoneware body made at GBP. When making pieces for the Anagama, it is essential to mix grog (firesand) with your clay since it makes the body stronger and better resistant to the harsh firing that is to follow.
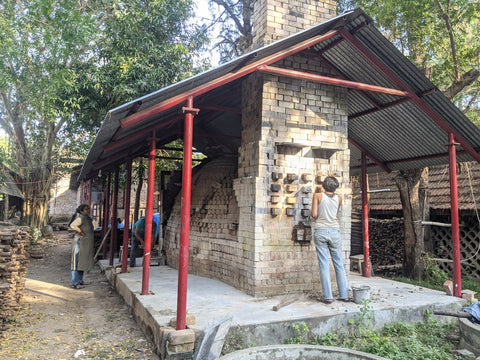
‘Anagama’ is a Japanese term for a cave kiln, it is fuelled by firewood and what essentially makes an Anagama kiln special is that there is no physical structure separating the stoking space from the pottery space. So the wood lands up burning right next to the pots during the firing. This makes our next step very crucial; The Loading.

Loading this giant kiln is the most important part of the process. Much of how smoothly the multiple day long firing goes is dependant on how the kiln is loaded. The placement of the pots direct how the flames will eventually move around the kiln, which would directly affect how the pieces come out looking. This makes the loading one of the most technically crucial part of the process. The potter must imagine the flame path as it rushes through the kiln, and use this sense to 'paint the pieces with fire’.
It took us three days to load up the kiln in three segments; the back, the middle and the front stack. The pieces are loaded on tiny balls of wad clay, which is a mixture of fire clay, grog and rice husk. Wadding the pieces helps in easily removing the pots post firing and in stack loading on the same shelf. Placements of the wads and the way the flames move around during the firing play a big role in the final aesthetics of the piece. Moving on to the most thrilling part of the process; The Firing.

It is necessary to spend a long time in firing to achieve the quality of the ware in an Anagama. Stoking occurs round the clock until a variety of variables are ticked off, these include the temperature reached and sustained, the amount of ash settled on the pieces, and the type of atmosphere created inside the kiln. The kiln has 7 stoke holes, 3 on each side and one main hole in the front, it also has active and passive dampers which help in controlling the firing atmosphere. Reading the flames, listening to the crackle and getting into the rhythm of stoking, there is a lot more to it than what the pyrometer shows.

We fired for 70 hours. A slow and steady temperature rise is maintained at first and then shifting gears to creating a reduction atmosphere in the kiln while maintaining the temperature rise and controlling the ash beds created between each loaded stack. Two people are needed around the kiln at all times, so our firing shifts were divided accordingly. Its really some feeling trying to control this hot radiating oven that is easily a size of a small room, my last shift on the third day of the firing landed up being 18 hours long. I never had imagined experiencing heat energy the way I did during that time. The thrills and chills of the process are definitely worth it. Around the 60th hour we did an impromptu Hikidashi, this is when a flaming hot piece is pulled out during the firing to see the ash buildup and glaze melt. Also proving to be a great adrenaline rush provider.
Once the desired temperature was reached and sustained, when the kiln is usually closed off completely at this point, we had planned to experiment with another firing process called Down Firing. This is when you do a controlled cooling of the kiln while smoking it till a certain temperature drop. Smoking atmosphere is achieved by first minimising the air supply in the kiln by shutting the chimney and closing all the air vents and then damp wood is stoked. This causes the smoke to be trapped inside the kiln and which results in smoke trapping in the glazes and also affects the glossiness and body flashes on the pieces. It is essential to always keep experimenting, we weren't sure exactly what is going to happen but I’m glad I got to experience this side of the firing as well. And finally after a few hours of down firing we put the kiln to rest and let it cool down at its own pace, it was time for us to cool down as well.

It took the kiln three days to cool enough for us to brick down the front door and finally see what all the madness had resulted in. The days before that go in resting out the heat exhaustion and getting lost in the anticipation of what might the pieces land up looking like. Truly a great patience tester.
In mist of all the ash and debris, there is a great sense of relief felt when you see all the pieces standing in their final stage. I always find unloading days a bit overwhelming, seeing all the results for the first time all at once just feels like too much to process in one go but that doesn't affect the excitement of getting everything out.
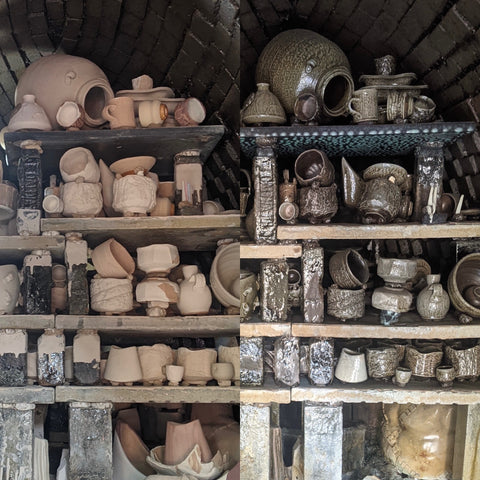
70% of all the pieces that had gone in were unglazed on the outside, and thats the beauty of the Anagama Firing, that it results in its own natural glaze layer forming with oh so many variations throughout the kiln. Wood-fired pots are admired for the evidence they bear of searching flames, intense heat, incidental ash deposits and scars from surrounding pots. The extra glaze is created by the wood-ash fluxes

The Anagama special formula
Flame + Ash + Clay body minerals = Natural Ash Glaze
Along with heat, burning wood produces fly ash and volatile salts which settle on the pieces and create all these crazy variations. All the pieces that you see here in the photos were loaded just by itself without any glaze on top and they've come out looking this way all because of the firing. How amusing is that!


There is so much movement and energy captured in each of these pieces that every side lands up telling a story about what it has been through.

With every new experience there is so much to take out of it. Just the willingness to learn and the openness to keep experimenting can take you a long way. Super grateful for the Co-firers and my mentors Aarti Manik and Khanjan Dalal for letting me be a part of this and Ray Meeker for guiding us through. Pulling this off wouldn't have been possible without the help of all the kind staff at Golden Bridge Pottery and Abhida.
